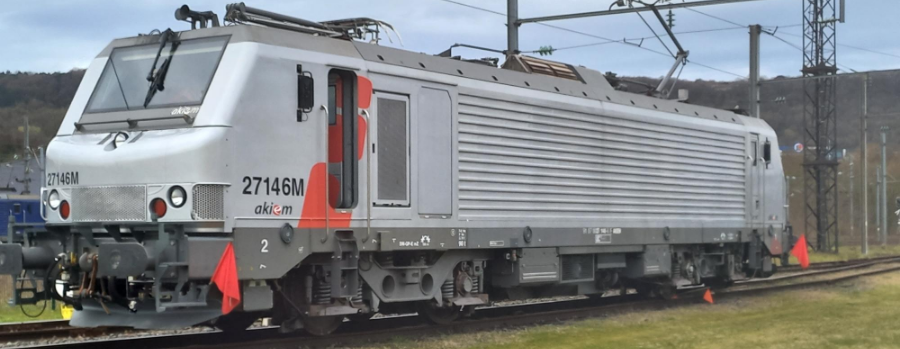
With its MLO programme, Akiem is taking its future in hand
MLO (Mid-Life Operations). These three letters stand for an industrial programme on a scale never previously attempted by Akiem. It involves 153 Prima BB27000 and BB37000 locomotives, together accounting for around 20% of the entire group-managed fleet.“ These locomotives were built between 2003 and 2009,” explains Renaud Brassart, Head of the Prima Overhaul Programme at Akiem’s Maintenance & Services branch. “They now need a major overhaul to keep them in commercial service for at least another ten years.”
In the past, Akiem always relied on contractors such as Alstom and Masteris to deliver every aspect of this type of operation, but it has now decided to carry out the complete overhaul programme entirely in-house. This is a major undertaking, as well as being one of the deciding factors behind the decision to greenlight construction of the workshop at Ostricourt. So, what are the benefits can we expect to see? “Better control over timescales, costs and the quality and productivity criteria applied to overhauling Prima-class locomotives,” says Renaud Brassart.
Greater satisfaction from our customers, who will have access to locomotives that have been overhauled to a high standard and deliver higher levels of reliability and availability than before
Creating every procedure from scratch
The Krefeld workshop in Germany is currently involved with overhauling some locomotives (Traxx, Vectron, etc.), but this involves pre-existing maintenance plans that our teams know inside out. The team leading the MLO programme had to start with a blank sheet of paper and create every procedure from scratch: tests, methods, logistics, scheduling, and all the rest. “The lack of any pre-existing maintenance plan was one of the biggest obstacles we faced,” explains Nicolas Dupret. “Working with an outside consultancy, we meticulously compiled a list of items to inspect, overhaul and renew, as well as drafting detailed specifications for how tasks are to be carried out.” Feedback from experience gained on the first locomotives will be used to make any further adjustments that may be needed.
Industrial quality was another area that provided a test of the ability of Akiem’s teams to adapt, requiring multiple inspections of revised or newly installed components, supplier warranties, etc. All of this meant rolling out stricter processes on a scale unlike anything Akiem has known in the past. The shift to performing major overhauls in-house represents a massive step forward for Akiem, and is something that will give us a head-start over the competition. We will be the only player in the French rolling stock leasing market able to carry out 100% of these operations in-house.
Just eight weeks to overhaul a locomotive
Once the MLO programme is operating at full capacity, four locomotives will be overhauled simultaneously. Around 60 separate items on each unit will be overhauled: brake modules, pantograph, high-voltage circuit breaker, etc. The volume of components means Akiem had to turn to a large panel of suppliers.
When we were inviting suppliers to tender, we always preferred partners that offered reliable solutions without unnecessary high quality, in an effort to keep prices under control. During this selection phase, we made countless visits to potential suppliers to audit their working practices, quality control systems and the types of equipment used
Akiem has set itself an eight-week turnaround target for locomotive overhauls. This is quite a challenge! “Controlling logistics flows is key to our ability to meet deadlines,” says Renaud Brassart. To achieve this, all the companies involved in overhauling individual components have signed binding contract clauses. For instance, no more than 10 days are allowed from the moment a part leaves the railway workshop until it is returned fully overhauled and ready to be installed by our fitters.
A programme that brings our teams together
A programme on this scale requires regular contacts between all of Akiem’s specialties and departments. The teams at Maintenance & Services and Locomotive leasing have to work together to adapt their respective requirements and constraints so that they can agree timetables for collecting locomotives for overhaul from customers, and dates when they will be returned. And the procurement team acts as the interface between suppliers and in-house teams.
“Having locomotives out of action for extended periods can also be an opportunity to make progress with other tasks,” according to Samia Saadaoui and Elias Charles. “We are currently working very closely with Locomotive leasing teams to improve synchronisation between mid-life operations and boogie maintenance.”
What is the current operational status of the MLO programme? Until the Ostricourt workshop is delivered in 2024, all locomotive heavy maintenance is carried out at workshops belonging to our partner Hiolle Technologies. Two locomotives have already returned to service and three more are currently being overhauled. “The unit that acted as a prototype had been out of service for eighteen months. It has now been operating trouble-free for over two months, with no alarms and no breakdowns,” says Renaud Brassart. This is a promising sign for the next phases of a programme that will run all the way until 2029.
Primas modernised with upgraded equipment
Akiem is keen to make good use of the time its Prima locomotives are out of service to update them to modern standards in areas not covered by the maintenance plan. For example, driver compartments will be repainted and fitted with USB sockets, and exterior halogen lights will be replaced with LEDs. Some items affected by problems of reliability or obsolescence — such as air compressors, consoles, cockpits and traction control valves, etc. — will be replaced or upgraded. This is also an opportunity to standardise the appearance of our fleet by applying the Akiem livery to every locomotive, meaning they will exit the programme looking brand-new in every way!